Keywords: electric vehicles, portable charging connector, charging devices
Most pure electric vehicles are equipped with portable charging guns to facilitate owners in charging their vehicles using 220V mains electricity, which falls under the category of slow AC charging. The slow charging system of new energy vehicles utilizes 220V single-phase AC electricity as the power source. Through the onboard charger, the AC electricity is converted into high-voltage direct current to power the traction battery.
The current path is as follows: 220V mains socket → portable charging gun → vehicle AC charging port → onboard charger → traction battery. This article focuses solely on the portable charging gun, analyzing its structure and charging principles, and provides solutions to common issues encountered during its usage, serving as a reference for vehicle users and after-sales service technicians.
- The structure of a portable charging gun primarily consists of the charging gun head, high-voltage charging cable, cable-mounted control box, and 220V three-phase plug. The gun head typically features a mechanical lock latch and unlock button to prevent detachment from the vehicle charging port during charging.
The AC charging port of new energy vehicles features a 7-pin structure, as shown in Figure 2, with the definition of each terminal corresponding to Table 1. Most charging guns have both mechanical and electronic locks. Pressing the mechanical lock button on the gun head raises the mechanical lock latch. After inserting the gun head into place, releasing the mechanical lock button causes the mechanical lock latch to engage with the mechanical lock slot on the vehicle’s charging port, ensuring the charging gun remains securely attached. When the vehicle doors are locked using the car key, the electronic lock of the charging gun is activated. At this point, the electronically controlled lock pin extends outward, inserting into the electronic lock hole and pressing against the mechanical lock latch, preventing it from disengaging from the lock slot. Consequently, the charging gun cannot be removed from the charging port. Pressing the unlock button on the car key retracts the electronic lock pin from the lock hole. Only then, by pressing the mechanical lock button, can the mechanical lock latch disengage from the lock slot, allowing the charging gun to be removed. Therefore, the presence of the electronic lock is to prevent malicious removal of the charging gun during the charging process, a functionality absent in vehicles lacking an electronic lock for the charging gun.
The operational principle of charging with a portable charging gun involves a series of steps.
When the three-phase plug is inserted into the 220V socket, detection point 4 in the power supply control device detects the socket’s ground wire through the grounding terminal on the plug (detection point 4 is grounded, causing a voltage drop). At this point, the S1 switch is toggled to the +12 position, resulting in a voltage of around 12V between the charging gun’s CP and PE. Grounding serves the purpose of leakage protection. Currently, the majority of portable charging guns are equipped with leakage protection functionality, with only a few early models lacking this feature. Charging guns with leakage protection functionality must be plugged into sockets with ground wires (detection point 4 detects the ground wire, causing a voltage drop) to function properly; otherwise, they cannot charge normally.
S3 is the mechanical lock button on the charging gun, acting as a normally closed switch. When the mechanical lock button is not pressed, S3 is closed, shorting R4. However, when the mechanical lock button is pressed, S3 opens, and RC is connected in series with R4. Before the charging gun is inserted into the vehicle’s AC charging port, there is always a voltage of around 5V between CC and PE of the charging port. In other words, when the gun is not inserted, the voltage at detection point 3 in the vehicle’s control device is approximately 5V.
During the process of pressing the mechanical lock switch to insert the charging gun into the vehicle’s charging port, the PE terminal at the gun end makes contact with the PE terminal at the charging port first, grounding to the vehicle body (chassis). Subsequently, the CC terminal at the gun end makes contact with the CC hole at the charging port. Detection point 3 is connected to the vehicle body ground through RC and R4, causing the voltage to drop to U1 due to these two resistances. Consequently, the vehicle’s control device determines that the charging gun is in a semi-contact state at this time.
Simultaneously, the CP terminal at the gun end also makes semi-contact with the CP hole at the charging port. The power supply control device detects this connection via detection point 1 → the CP terminal in contact → R3 connected to the vehicle body. As a result, the voltage at detection point 1 drops, prompting the switch S1 to toggle from +12 to PWM position. The power supply control device then provides a pulse signal to the vehicle control device, following this path: power supply control device PWM terminal → S1 → R1 → CP → D1 → detection point 2 → vehicle control device.
This signals the charging equipment to enter the ready state. After the charging gun is fully inserted and the mechanical lock button is released, S3 closes, shorting R4. At this point, the resistance connected to the CC and PE terminals is reduced to only RC, resulting in a decrease in resistance. The voltage at detection point 3 changes from U1 to U2, indicating to the vehicle control device that the charging gun is properly inserted.
After confirming the charging demand of the traction battery, the absence of faults in the traction battery and onboard charger through the onboard network (CAN network), and closing S2 relay switch, the vehicle signals its readiness for charging. Upon closure of S2, R2 is incorporated into the R3 circuit, altering the pulse signal at detection point 1. The power supply control device interprets this change as confirmation of the vehicle’s readiness and closes K1 and K2, supplying power to the vehicle end, as shown in Figure.
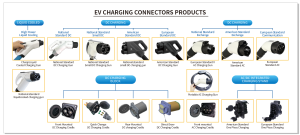
3.Analysis of Common Issues in Slow Charging for New Energy Vehicles
3.1 Troubleshooting when unable to charge using a portable charging gun.
(1) If the socket lacks a ground wire, the charging system enters a leakage protection mode, causing K1 and K2 to disconnect, thus preventing charging. Method of determination: Firstly, refer to the flashing pattern of the warning light on the cable-mounted control box (as detailed in the vehicle manual). Secondly, insert the three-phase plug into the 220V socket and use a multimeter to measure if there is a voltage of around 12V between the CP terminal and the PE terminal of the charging gun head (AC or DC?). If present, the socket has a ground wire; otherwise, it does not.
(2) If the S3 switch is damaged and cannot close, detection point 3 continuously detects the resistance of RC + R4, always indicating that the charging gun is not properly inserted (in a semi-contact state), and thus cannot send a charging ready signal. Method of determination: With the power off, use a multimeter to measure the resistance between the charging gun’s CC terminal and the PE terminal. The resistance before and after pressing the mechanical lock button should differ. If not, the S3 switch is damaged.
3.2 Is the charging speed the same when using different charging guns for the same vehicle?
The answer is it may vary. The key factor determining the charging speed of the charging gun is the RC resistance, which determines how much charging current the charging gun can output to the vehicle. Table 2 shows the RC resistance (resistance between the CC terminal and the PE terminal when the mechanical lock button is not pressed) and the rated output current of different brands/types of charging guns. From the table, it is evident that whether the charging speed is the same when using different charging guns for the same vehicle depends on whether the RC resistance is the same.
3.3 The rated output current of the charging gun does not necessarily equal the actual maximum charging current; the actual maximum charging current also depends on factors such as the power of the onboard charger and the condition of the traction battery. For example, when using a slow charging station with a rated output current of 32A to charge a vehicle, if the vehicle’s onboard charger cannot handle such a high charging current, the actual maximum charging current will be less than 32A.
In conclusion, there are many reasons for AC charging failures in new energy vehicles. Apart from considering faults in the charging gun’s circuitry, one must also consider faults in the vehicle’s charging-related circuits. If any of these circuits have a fault, the charging system will be unable to charge the traction battery properly. Therefore, whether one is a newcomer studying new energy vehicle maintenance technology or an experienced technician, it is essential to have a clear understanding of the system control principles before troubleshooting. This understanding enables accurate analysis of the root cause of the fault and facilitates the quick identification of the faulty component.